在国家重点研发计划“新能源汽车”专项支持下,历时4年,长安汽车第一个碳纤维-铝合金混合结构车身成功试制下线!
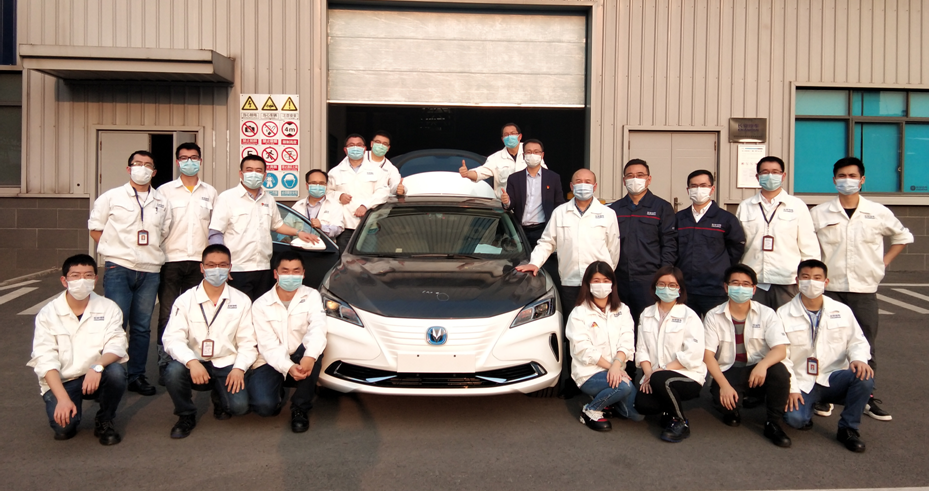
长安汽车组建矩阵式项目团队,以院士、行业专家领衔的多支研究团队合作进行高效研发。4年来,研究人员突破了诸多技术门槛,不断创新研究,通过使用航空级碳纤维和铝合金,同时集成超高强钢、镁合金、异种材料连接等前沿技术,数经十项测试验证,实现了高强度与轻量化完美集成,并提升了安全性能,极致地引领国内自主研发项目,实现了车身与底盘共减重≥30%、比同级车型减重200kg的目标,项目将首次实现碳纤维车身的CN-CAP五星碰撞的要求。
本项目通过运用轻质材料、新型结构设计,开发出了一款碳纤维车身纯电动轿车,这一突破性壮举将助推中国汽车碳纤维、铝合金、镁合金等产业快速发展。
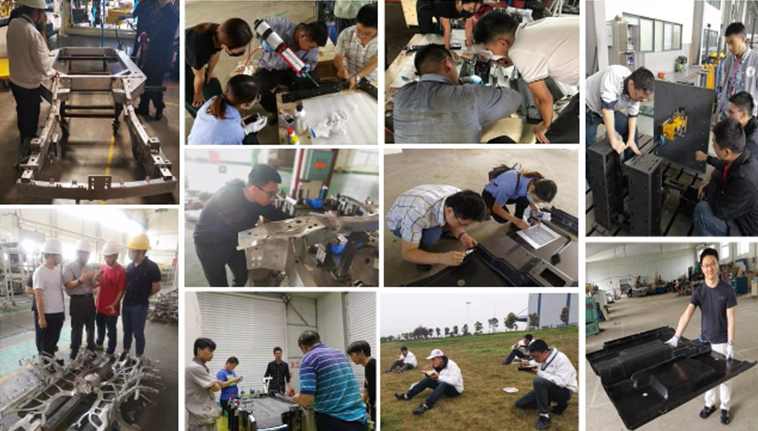
碳纤维复合材料的使用,若按照全行业年产销40万辆新能源汽车,单车碳纤维用量 70kg计算,共需碳纤维约 2.8万吨/年,每公斤按120元计算,大约形成33.6 亿元产值经济效益;碳纤维复合材料零部件的使用,按照240-400元/公斤计算,预计形成67-112 亿元产值经济效益;若按照整车售价15万元/辆计算,预计每年可新增约600亿元产值的经济效益。本项目开发的铝合金前后碰撞横梁、控制臂、转向节等零件、镁合金转向支撑、座椅骨架等零件还可以应用在长安同级别的传统燃油车上。若按照年产20万辆、轻质合金零件的价值0.5万/辆计算,可形成年产值约10亿元的经济效益。
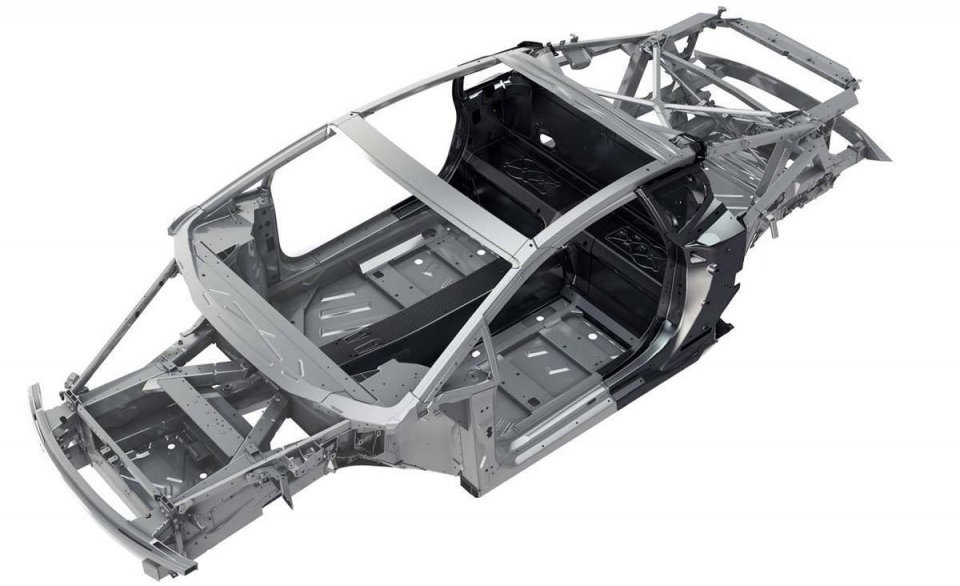
不仅如此,单车实现了减重200kg,百公里电耗可降低0.5-0.6kWh目标,若按照单车每年行驶3万公里,每年电能消耗将减少72亿kWh来计算,可为节能减排事业做出重要贡献。
本专项的研究成果,还辐射到了轨道交通、能源、石油化工、船舶、建筑等其它相关领域,这带动了一批显示度大、产业带动性强和附加值高的高新技术产品以及行业的技术进步,拉动了国产碳纤维、铝合金上下游市场和需求,将新增万亿级的产业价值链,社会经济效益极为可观。
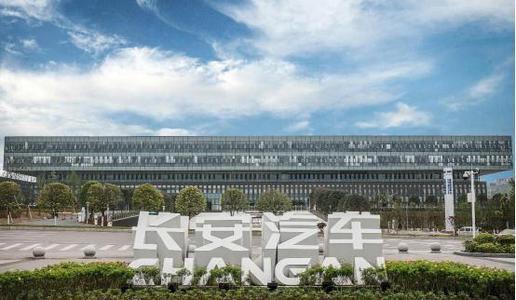
邢车博士工作室

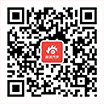
更多汽车资讯,涨知识赢好礼扫描二维码关注(auto_sina)