南山汽车产业基地内,一座全球化、高端化、智能化的工厂正以每90秒下线一台新车的速度进行生产,这便是领克汽车张家口工厂——吉利集团投资125亿元打造的全球标杆生产基地,也是吉利集团在北方最大的整车工厂。
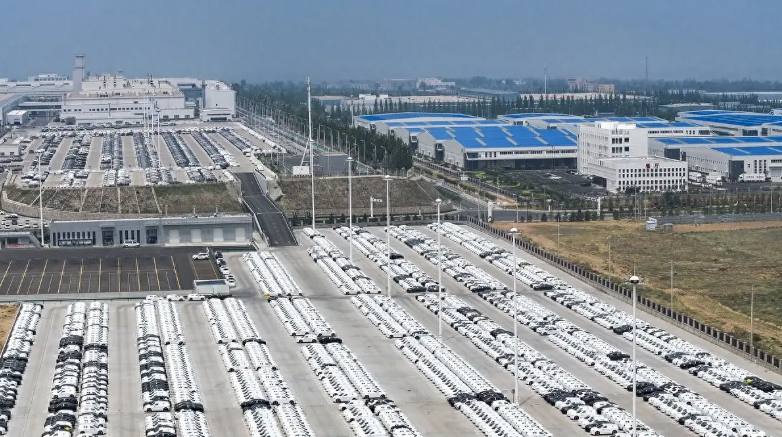
走进领克汽车张家口工厂,一场充满科幻感的自动化生产场景正在上演:焊装车间里,庞大的机械臂灵活摆动,根据生产需求协同完成车身焊接、部件装配等多个关键任务;总装车间内,无人导引车来回穿梭,进行物料搬运和配送,工厂内部物流运输更高效……通过数智赋能,物流配送速度和综合生产效率显著提升。2024年该工厂全年生产整车16.98万辆,同比增长89%;实现工业总产值241.5亿元,同比增长120%;纳税10.2亿元,同比增长64%;自2023年10月公司新能源车型投产以来,公司累计出口整车13.57万辆,累计出口额218.2亿元。
如今,数智化技术广泛应用带来的产业创新,正成为领克汽车张家口工厂培育和发展新质生产力的强劲动能。该工厂建有冲压、焊装、涂装和总装四大车间,四大车间完全基于“工业4.0”的理念规划,按照沃尔沃全球质量标准建设,通过引入完善的I T系统、采用先进的信息管理模式、配置一流的设备,实现智能工厂、智能生产和智能物流的目标,工厂的智能化、信息化、柔性化、自动化程度达到国际先进水平。
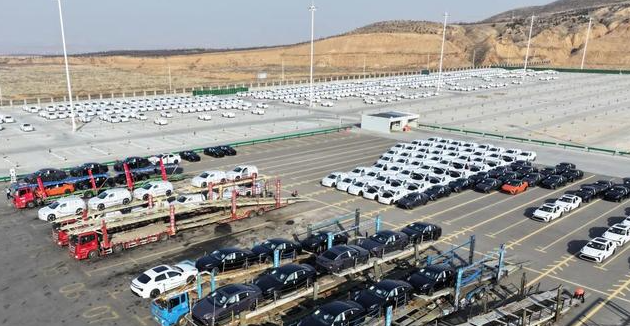
冲压车间规划建设两条高速冲压线,选用世界先进的多连杆高速机械压力机,以及世界先进水平的瑞士G U D E L最新二代单臂机械手,关键处覆盖件的模具从西班牙进口,模具采用进口的先进材料进行制造,并使用镀铬等国际领先涂层工艺处理,可以保证冲压件的高质量要求;焊装车间负责车身焊接与四门两盖装配及调整工作,是整个车身骨架构建的重要环节,车间拥有各种类型先进的自动焊接设备,使用世界顶级K U K A工业机器人,主焊线自动化率达到100%,最大可实现6款不同车型同时生产;涂装车间内,生产线机动采集信号,车型、颜色识别后实现自动配图,最大程度减少人员参与,在有效保证漆面质量,确保交付一流产品的同时,车间工业污水排放达到国家一级标准;总装车间拥有各种类型的先进装配设备,运用底盘整体合装技术和关键力矩信息化控制技术,在满足质量、节拍需求的同时,最大限度地提高人机工程。
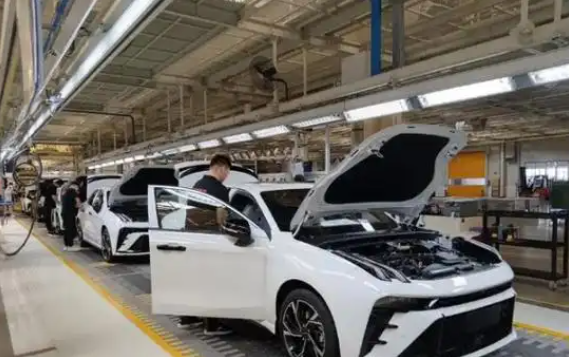
今年2月6日,吉利汽车与人工智能领域的D e e p S e e k宣布双方自研大模型完成深度融合,携手开展对星睿车控F u n c t i o n C a l l大模型、汽车主动交互端侧大模型等的蒸馏训练。届时,通过与D e e p S e e k的深度合作,领克能够快速获取先进的人工智能技术,将其应用于汽车的智能交互、智能驾驶等核心领域,从而加速产品的智能化升级。
人才是企业创新和发展的核心资源,当下的汽车产业对数智化复合型人才的需求愈发迫切,领克汽车张家口工厂聚焦新能源汽车和智能网联汽车高端化、智能化、绿色化技术升级,企业高瞻远瞩,着力实施“人才助力‘绿色+智能’汽车产业创新升级项目”,集聚国内外汽车产业高端人才、创新团队和高技能人才,为打造千亿级汽车产业基地提供有力人才支撑。领克生产线上的每名员工都要在领克学院接受半个月的学习培训才能到车间学习实操,通过一对一师带徒模式,员工再和师傅学习一个月,才能独立上岗。该工厂通过各种形式培养技术工人1.2万余人次,完成岗前培训1.2万余人次,在岗培训1万余人次,新型学徒培养1500余人次,以工代训培训1.5万人次,累计为当地解决就业1.3万余人次。记者 郝大钊 通讯员 高景山 丛晓日
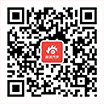
更多汽车资讯,涨知识赢好礼扫描二维码关注(auto_sina)
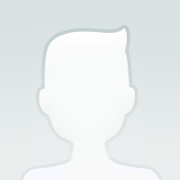
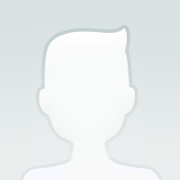